Quality control at Every Seam: Tank Welding Inspection Services Revealed
Quality control at Every Seam: Tank Welding Inspection Services Revealed
Blog Article
Comprehensive Container Welding Evaluation for Industrial Safety And Security and Regulatory Compliance
Making sure industrial security and governing compliance within the realm of storage tank welding inspections is an essential facet of preserving functional integrity and mitigating prospective dangers. The thorough evaluation of weld high quality, product thickness, and general container condition is critical in securing versus environmental hazards and structural failures. By delving right into the details of comprehensive tank welding evaluations, a deeper understanding arises of the complex methods utilized to maintain market criteria and promote safety and security methods.
Importance of Tank Welding Inspections
Carrying out complete and routine container welding examinations is essential in ensuring the architectural honesty, safety and security criteria, and governing conformity of industrial tanks. These inspections play an essential role in identifying any kind of possible problems or weaknesses in the bonded joints that can jeopardize the general integrity of the tank. By detecting these concerns early, firms can take aggressive procedures to address them promptly, therefore stopping expensive repairs, ecological contamination, or, in the worst-case situation, catastrophic failures.
Regular container welding assessments also aid organizations follow sector policies and criteria set forth by authorities such as the American Oil Institute (API) or Occupational Safety And Security and Health And Wellness Administration (OSHA) Failure to satisfy these demands can lead to fines, lawful consequences, or even the suspension of procedures. Tank Welding Inspection Service. Therefore, purchasing extensive container welding assessments not only safeguards the well-being of workers and the surrounding environment however also secures the company's credibility and bottom line over time
Trick Parts of Weld Top Quality Evaluation
Making certain the high quality of welds entails a meticulous examination of key components that add to the structural honesty and dependability of commercial storage tanks. One important facet of weld quality evaluation is the assessment of weld infiltration. Proper penetration is necessary as insufficient penetration can result in weld issues and endanger the strength of the joint. Additionally, the weld's profile must be analyzed to ensure that it meets the given demands in regards to dimension and form. The visibility of any gaps, such as splits, porosity, or incomplete fusion, must be thoroughly checked as these can deteriorate the weld and boost the chance of failing. Furthermore, the total weld look is also a key component of quality evaluation, as it can suggest the presence of issues or inconsistencies in the welding procedure. By adequately reviewing these vital parts, assessors can assist ensure that welded joints meet the required requirements for security and regulatory compliance in commercial storage tank building.
Product Thickness Analysis Techniques
In the context of weld top quality assessment, an indispensable element to consider is the application of material density assessment strategies. Exact dimension of product thickness is vital in guaranteeing the structural stability and safety of welded containers. Different non-destructive testing (NDT) techniques are used for evaluating product density, including ultrasonic testing, radiographic screening, and magnetic particle examination. Ultrasonic testing entails making use of high-frequency sound waves to establish product thickness by determining the moment considered the acoustic waves to take a trip through the material and show back. Radiographic testing uses X-rays or gamma rays to produce pictures revealing worldly density. Magnetic particle inspection works for detecting surface and near-surface problems that might influence product density. These techniques not only help in evaluating the thickness of materials however additionally help in recognizing any kind of potential defects or gaps that might compromise the weld high quality and general stability of the storage tank framework. By employing these product density assessment methods, sectors can make certain conformity with safety requirements and guidelines, therefore boosting total operational security and integrity.
Tank Problem Examination Methods
A necessary element in preserving the stability and safety of welded tanks is the thorough exam of container problems with reputable evaluation methods. Tank problem assessment techniques play an important role in ensuring the architectural stability and functional performance of commercial storage tanks. Regular inspections making use of these techniques are important for preventing disastrous failings and making sure the long-term integrity of welded tanks.
Benefits of Routine Inspection Practices
Routine evaluation methods not just protect versus potential problems detected during container condition assessment methods however also offer as aggressive steps in promoting the structural stability and functional performance of welded storage tanks. By performing regular evaluations, commercial facilities can determine any kind of indicators of corrosion, fractures, leakages, or various other defects in the tank welds immediately. This very early discovery enables prompt fixings or upkeep interventions, avoiding little problems from rising right into bigger, more costly problems that might endanger safety and security or lead to regulatory non-compliance.
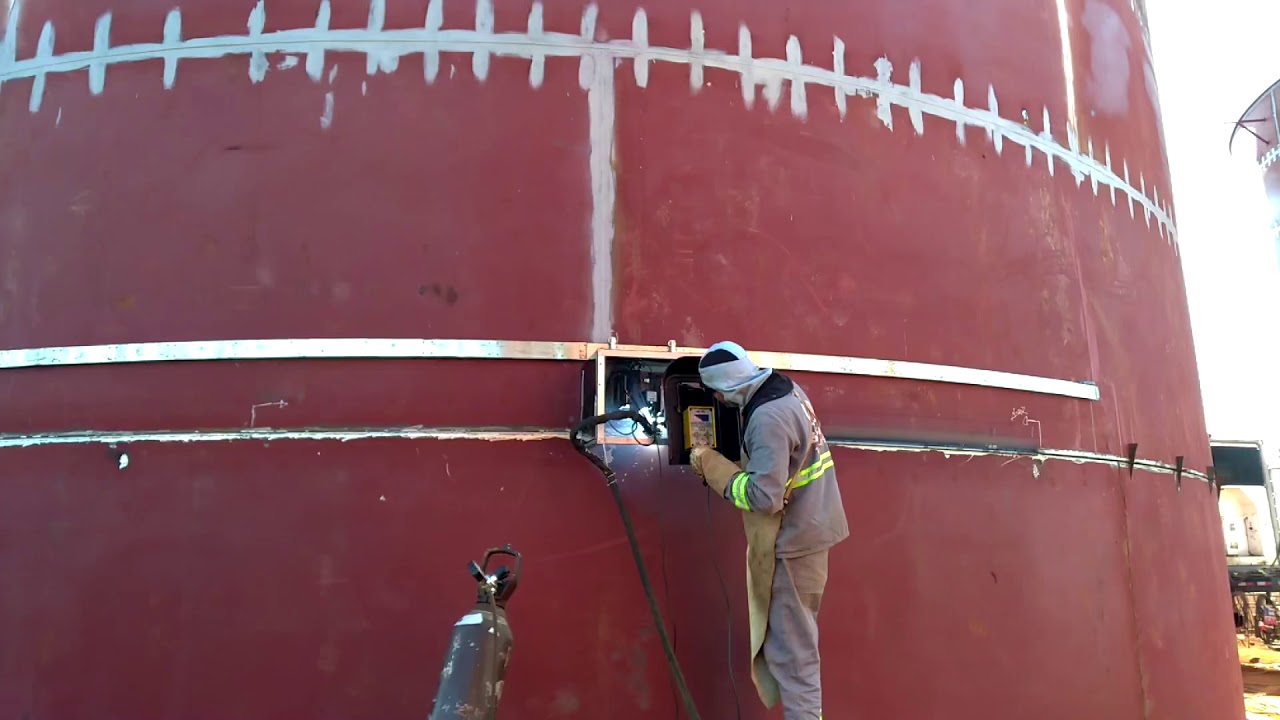
Conclusion

Finally, comprehensive storage tank welding examinations are important for making certain industrial security and governing conformity. By conducting routine examinations and analyses of weld high quality, product density, and tank condition, organizations can recognize possible risks and avoid expensive crashes. Implementing a proactive technique to evaluation methods can aid preserve the structural honesty of tanks, secure the setting, and make certain the safety of workers click this site and the surrounding community.
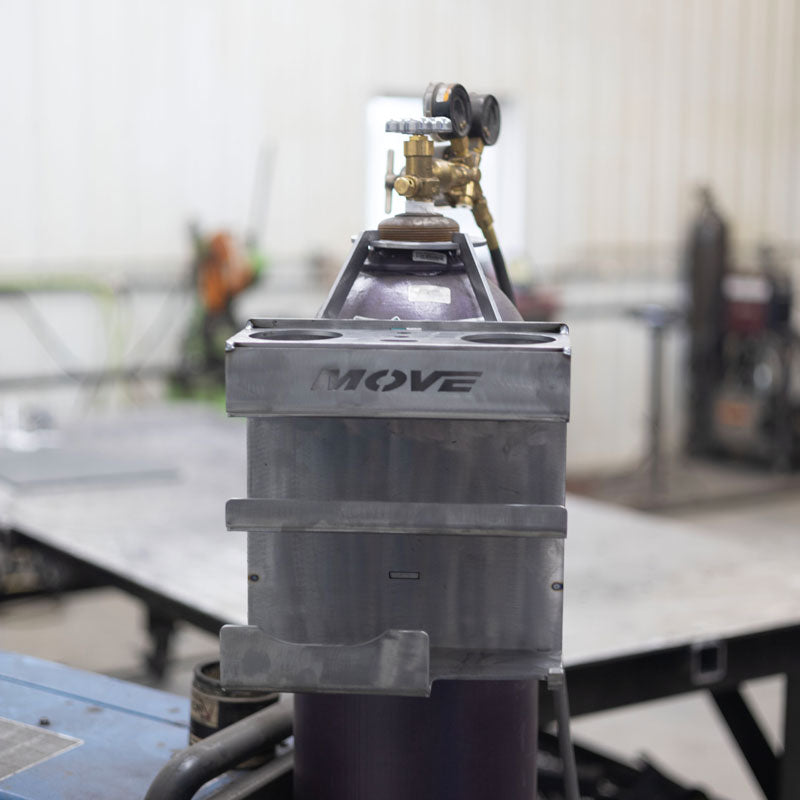
Report this page